Topic/Date | Overview | Who Should Attend | What You’ll Learn | Presenters
Design for manufacturability and assembly (DFMA) is a critical process that engineers can use to examine a product prior to (and during) manufacturing to look for opportunities for improvement and to ensure that it can be efficiently manufactured and assembled. This live workshop will introduce DFMA, some common design features you might see in a machine frame, and how to design those features into your frame for the best price and manufacturability.
More Webinar Details:
Topic: Design for Manufacturing and Assembly for Machine Frames
Date: Wednesday, May 4, from 1 PM to 2 PM EST
Press Release: Upcoming Webinar to Discuss DFMA for Machine Frames
Overview:
From meeting cost and specification requirements, engineers have a big undertaking when it comes to new products or the next generation of their product line. They are tasked with solving challenges so that design can be manufactured while ensuring quality control in the production planning stages before beginning any manufacturing process.
Unfortunately, some designers of sheet metal enclosures and assemblies do not consider the production process while designing their products. According to research, only half of small- and medium-sized manufacturers employ DFMA concepts. Statistics show that manufacturers spend over 40% of their time correcting errors, with 24% of those errors being directly related to manufacturability.
Without the engineer’s careful consideration of certain factors early on in product development, it is easy to get locked into expensive, difficult-to-manufacture sheet metal enclosure design. To help engineers navigate these considerations and deliver optimal product design, PEKO has prepared a webinar: DFMA Crash Course for Machine Frames.
DFMA initiatives can take place at different stages of the commercialization process but often prove most valuable following prototype efforts and scaling to “beta” or pilot units. Companies that follow DFMA guidelines are typically able to lower product costs, increase product reliability, and shorten the time to market.
Join us as we talk pro tips on designing machine frames and sheet metal enclosures with DFMA best practices in mind. Participants will gain an understanding of basic DFMA principles, common design considerations for DFMA on machine frames, the benefits and challenges of DFMA on machine frames, and how such challenges can be overcome with the successful adoption of the principle.
Target Audience:
Machine builders and designers who wish to gain an understanding of how they can incorporate DFMA principles into their machine frames.
Learning Objectives:
- Why DFMA is so important in product development
- Expert tips and tricks from a contract manufacturer
- Common fabrication and assembly checks
- How DFMA affects your design process
- How to solve DFMA issues during design
Presenters:
Mark Frosino, Sales & NPI Project Manager | LinkedIn
Mark has spent nearly 20 years at PEKO in the New Product Introduction (NPI) group. His primary focus is on the early-stage engagement of new customers to ensure that PEKO properly supports the development of their products and processes so that they can be successfully transitioned to PEKO’s production team for consistent, repeatable builds. In doing so, DFMA concepts have become a pivotal part of his NPI process.
Scott Baxter, Sales & Business Development Manager | LinkedIn
Scott has worked at PEKO since 2008. Recently, his attention has been drawn to the needs of DFMA for serialized repeated machine builds. Working with DFMA teams gives Scott a unique ability to speak to audiences of machine designers about their cost-down design struggles.
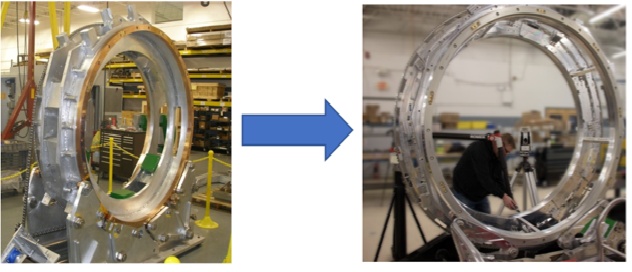