A production readiness review (PRR) is a critical step in the commercialization process. This step takes place when a project is expected to be ready to transition into PEKO’s production environment and processes. This review is a comprehensive examination by the project team and program manager of the design documentation, manufacturing processes, and functional specifications that have been completed for the product.
The PRR typically occurs when a) a project has been completed by PEKO’s NPI team and is scaling to larger, steady-state volume production, or when b) PEKO accepts an order to build a product that’s already established. The PRR helps to mitigate certain risks associated with new production builds by determining:
- If the product design is mature and ready to transition to production, from the standpoint of completeness and manufacturability.
- If production planning (i.e., facilities, tooling, and test equipment capacity, personnel development and certification, process documentation, inventory management, supplier management, etc.) was adequate.
PEKO has a team of qualified experts that will perform the PRR with a particular focus on engineering and manufacturability in order to lay the groundwork for successful production builds.
What’s the Purpose of a PRR?
The purpose of the production readiness review is to determine if the information provided by our customer or developed internally within PEKO will support the consistent and reliable production of a product that is both manufacturable and can meet its intended design and function. There are likely changes and revisions that occurred during the first build that can be addressed during the review and implemented to save time and money before production manufacturing takes place. Quality objectives are also verified during the review, including a completed factory acceptance testing (FAT) process and documentation.
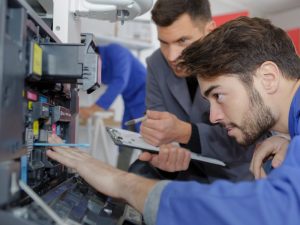
The production readiness review also allows PEKO to assess the need for additional resources necessary to complete the build, including items such as custom equipment and properly trained personnel. With our competent, cross-trained team of technicians, resources can be deployed as demand increases or decreases.
We maintain an employee competency matrix to ensure that proper skill sets are achieved and maintained and that the right resources are allocated. Beyond personnel, we have an enormous capacity including over 375,000 sq. ft. of manufacturing space and 120+ machining centers across nine buildings to support your product’s manufacturing and production needs.
What’s Examined During the Production Readiness Review Process?
- Mechanical print packages
- Electrical schematics and layouts
- BOM accuracy and completeness
- Work instruction development and review
- Production planning documentation
- Existing and planned facilities
- Tooling, fixtures, and test equipment
- Manufacturing methods and controls
- Assembly sequence and workflows
- Takt time and delivery rates
- Quality control and assurance provisions and documentation