Controlled Environments for Precision Assembly of Clean-Critical Applications
Are you sourcing a high-dollar program that requires hundreds or thousands of clean room assembly hours per year? PEKO offers clean room assembly services to OEMs with recurring, high-precision programs that demand both technical accuracy and contamination-free environments. Our ISO 6 (Class 1000) clean room supports the assembly of mechanical, electromechanical, and optical systems for regulated and high-performance industries.
- 12,000 square feet of Class 1000 Clean Room (ISO 6) certified space
- Assembly and packaging of systems requiring particle and microbial control
- Supports medical, semiconductor, and aerospace-grade applications
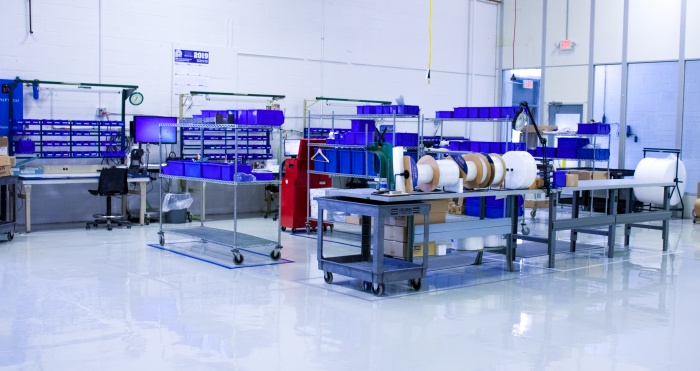
What Sets PEKO’s Clean Room Assembly Services Apart from the Rest
- Built for Subsystem Integration, Not Just Components → PEKO specializes in assembling functional subassemblies and finished systems, not just cleaning and bagging parts.
- Mechanical + Electromechanical Capabilities → We integrate motion systems, wiring, brackets, and more within a controlled environment.
- Full Program Management → From design collaboration to packaging and delivery, PEKO handles the full lifecycle of clean-room-sensitive assemblies.
Learn More About Our Facilities
Why Leading OEMs Choose PEKO for Their Clean Room Assembly Requirements
- Strict Particle & Contamination Control → Our clean room follows rigorous gowning, filtration, and cleaning protocols to protect sensitive builds.
- Compliance with Medical & Semiconductor Requirements → PEKO supports industries that require traceability, validation, and documented handling procedures.
- Controlled Packaging & Logistics → Products are bagged, sealed, and labeled in clean environments to maintain protection through shipment.
- Need to Offload Controlled Assembly from In-House Operations → OEMs turn to PEKO when internal facilities aren’t equipped for clean assembly, or when they need to free up production resources.
Our Clean Room Assembly Process
- Engineering Input & Workflow Planning → We work with customer engineering to ensure layout, handling, and process flow meet cleanliness needs.
- Pre-Clean & Prep Outside the Room → Hardware is wiped, staged, and verified before entering the clean environment.
- Clean Room Assembly & Integration → Operators assemble systems using clean-compatible tools and approved methods.
- Inspection, Bagging & Labeling → Finished assemblies are inspected, double-bagged, and sealed for protected transport.
- Controlled Fulfillment & Delivery → Items are shipped per customer instructions, including bulk or single-kit boxing and discreet delivery.
Industries & Applications
Our clean room assembly services support OEMs building high-specification equipment:
- Medical & Life Sciences → Enclosures, panels, and modules for regulated diagnostic devices
- Semiconductor & Electronics → Precision hardware for fab tools and clean-adjacent integration
- Aerospace & Defense → Ruggedized enclosures assembled in particle-controlled conditions
- Optics & Instrumentation → Sensitive lens systems and motion assemblies requiring contamination control
Let’s Build Together
Whether you need a partner for regulated medical builds, clean-adjacent semiconductor systems, or contamination-sensitive optics, PEKO offers both ISO 6 (Class 1,000) and ISO 7 (Class 10,000) clean room assembly options with full program support. We help OEMs free up internal clean room resources, maintain compliance, and bring high-precision assemblies to market—clean, sealed, and ready to perform.