Engineers, product, managers, and new product development teams face early-stage challenges that most people don’t realize. Not only are they juggling design, functionality, durability, and other product-related issues, there is a manufacturing issue on the horizon.
The ultimate goal of most organizations engaging in new product development is to work through the commercialization process and into repeatable full-rate production manufacturing. With this goal in mind, Design for Manufacturing and Assembly, also known as DFMA, will be part of the equation.
From the perspective of a contract manufacturing company, this is easier said than done. Looking through PEKO’s portfolio of startups and new product development projects that have come through our door, I’d estimate that 95% or more new products that come across our desks require some form of DFM.
The fact is, not all engineers are well versed in such a design feature. One primary reason for this is the natural chasm between job functions. Mechanical and other engineers in today’s world of outsourced manufacturing are typically separated from the dozens of processes that are required to build their designs.
Let’s face it. Can a design engineer reasonably be expected to know all the setup times, tolerance capabilities, associated costs, and other nuances associated with every part he/she designs for all of his/her available vendors? What about the other processes, like assembly, plastics, coatings? The answer is a resounding no. Especially when they are just trying to get the thing to work!
So, let’s take a look at a few popular questions we hear:
- What is Design for Manufacturing (DFM)?
- How do I incorporate DFM into my product?
- What are the advantages to DFMA?
- What are some common issues when applying DFMA?
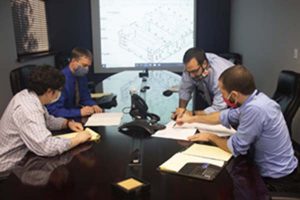
Engineers discussing cost down DFMA engineering
What is DFM (Design For Manufacturing)?
I fondly remember my Design for Manufacturing and Assembly class back in college. The final project was to take a random household object, apply concepts of DFMA, and redesign it to create the most efficient and cost-effective design. In my case, I chose a cheap table fan. I was able to reduce the estimated cost and part numbers by around 30%. Not bad for not even having access to the drawings.
The object of Design for Manufacturing and Assembly is to design your product in such a way that ease of assembly is increased, and ease of part manufacture is also increased. In other words, we want the parts to be simply made and assembled together. This translates to lower costs, quicker time to market, and other process and business benefits that I will discuss later.
It’s important to note that DFMA, DFM (Design for Manufacturability), and DFA (Design for Assembly) are all interrelated, and you may see people in the industry using them interchangeably, however, this is not completely accurate. DFMA is a combination of both DFM and DFA, encompassing the parts manufacture and the assembly processes.
How Do I Incorporate DFM and DFMA Into My Product?
Of course, this is the million-dollar question, and we’ve touched on it in a previous blog post. Most people learn how to apply DFM and DFMA concepts into their design by taking college-level courses, or by good old-fashioned industry experience.
Generally speaking, DFMA looks at many factors but here are three groupings that we like to lean on:
- Eliminate – look for parts that aren’t even necessary to the product function. You’ll be amazed at the amount of redundant or even useless parts that end up in a design. There are a lot of reasons for this, like design changes, new engineers, and features that never took hold.
- Combine – this is one of my favorites. During early phase development, engineers are oftentimes just trying to get the product to function correctly. Standoffs, adapters, plates, bushings, clips, brackets, and other parts find their way into a design. But in a DFMA project, the re-design must consider that in a production environment, new parts and processes can be incorporated. A great example is plastic molding or casting, where you can take an assembly of multiple parts to create surfaces and features and replace it with a larger part that can be easily molded with the features, faces, and bosses incorporated directly into it. It will be easy to produce and will have a huge effect on lowering assembly time
- Optimize – Can the parts be simplified? Can assembly be simplified? Here are three great ways to optimize the assembly process. 1) Create modular sub-assemblies that can be easily built outside of the final integration 2) Are there easier ways to join the parts, like using clips, tabs, or press-fitting versus screws, nuts, and bolts 3) are the parts optimized with orientation in mind? Can they only be assembled in one direction, so the assembler doesn’t have to fumble through it or risk assembling backward? This can be done with keyways, bosses, asymmetrical features
Of course, another way to incorporate is to hire a firm with engineers on staff that have a crossover knowledge of design and manufacturing techniques. From what I’ve seen, this is probably the most common method. Designers lean on both consultants AND the actual parts manufacturers for feedback in the DFM arena. Manufacturers are great at coming back to the design team with some simple suggestions like tolerance selection or material availability, to make the part (and their lives) easier, and usually know the costs of doing so.
What Are the Benefits of Incorporating DFMA Techniques into My Design?
Design for Manufacturing and Assembly addresses many major business and manufacturing concerns when it comes to the benefits it provides. In any major development or manufacturing system, we’re concerned with Cost, Quality, and Delivery. DFM at the parts level aims to lower costs by using material, process, and geometry optimization. The costs involved in certain parts or buried secretly in their design in those three categories. This means looking at alternatives for each category and pairing it with your functionality and production volume needs.
I’ve seen material changes with zero functionality impact yield over 40% just because the designer basically used the “material they’d always used” from previous designs. Quality concerns are positively impacted with good DFMA treatment because reducing hardware and improving orientation at assembly will drastically reduce reworks and rejects at the line level. And of course, with quality impacts and efficient design selection, you’re going to see lead times drop accordingly.
What Are Some Common Issues for DFM and DFA?
With all the great benefits from DFMA and DFM, one wonders what are some common issues that might crop up?
First and foremost, finding the right people to help with DFMA is somewhat difficult. The crossover experience for materials, processes, quantities, and techniques is extremely broad. Industrial professionals with a broad skill set across many techniques are difficult to come by. One great way to overcome this is to involve your parts manufacturers at an early design stage. They can give their guidance to some degree.
Another common issue we see is that DFMA does add some initial time and energy in the early stages when the product time might be on a deadline. There can be time and money associated with undoing some designs that are already complete, retooling a manufacturer, remaking parts, and seeking approvals for already-designed parts.
Lastly, is fear. Nothing is guaranteed. Even the best DFMA treatment will have some confidence level associated with it. In other words, not every Design for Manufacturing and Assembly idea will have the impact that was planned. Anything can happen in design and manufacturing and there are plenty of ways to the top of the mountain.
So, is Design for Manufacturing worth the cost of admission? In my opinion, yes. From experience, most companies that walk through the door are looking for DFMA in some fashion, even if they are using different names to describe what they need (cost downs, engineering suggestions, optimization).
I’ve outlined what is DFM(A), how to get it incorporated into your product, and what are some benefits and issues. With any luck, you can start your DFMA journey here. Feel free to reach out to PEKO to see our DFMA services and how we’ve incorporated major changes to help our customers get to market faster with long-lasting and high-quality Contract Manufacturing methods.