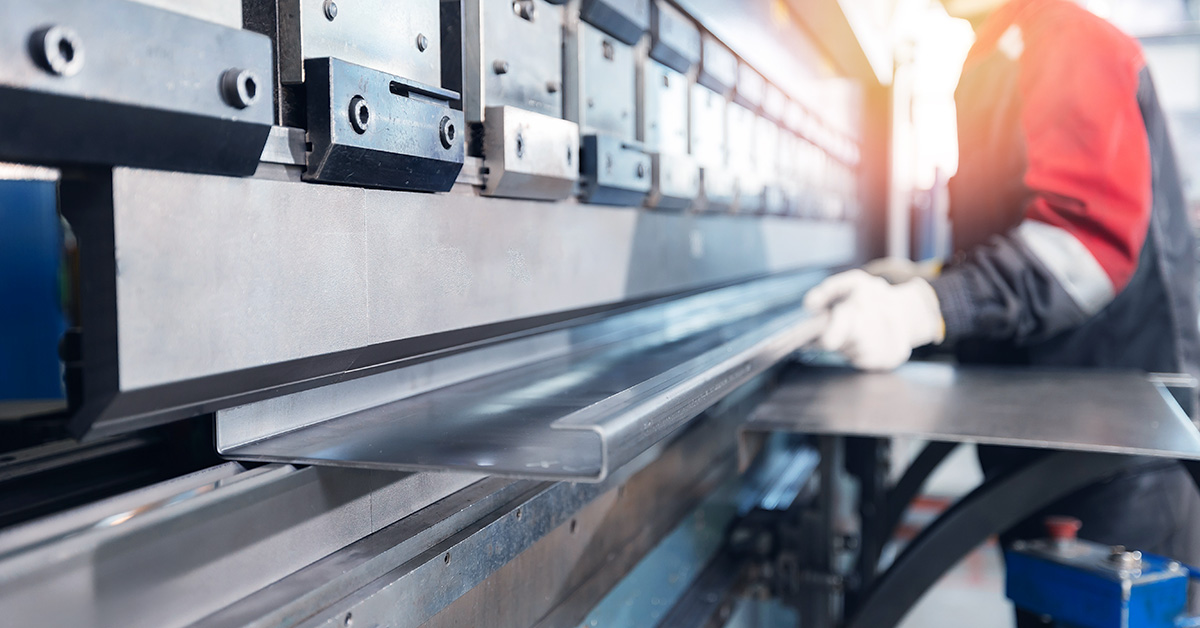
In sheet metal fabrication, one of the critical factors engineers must account for when designing parts is bend allowance (BA), also known as stretch allowance. Metal stretching occurs when the sheet metal undergoes bending, forming, or drawing processes, and it can significantly affect the final dimensions of the part. Accurate calculation of sheet metal bend allowance is essential to ensure that the part maintains its intended shape and meets the design specifications. This blog will explore the concept of bend allowance, how to calculate it, and provide guidelines for considering it during sheet metal operations.
What is Sheet Metal Bend Allowance?
When sheet metal is bent or formed, the inner surface of the metal undergoes compression, while the outer surface is stretched.
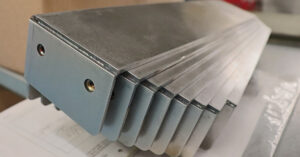
Sheet metal bend allowance refers to the extra length required to compensate for this stretching, ensuring that the final dimensions of the part are accurate. Stretching happens due to the nature of the bending or forming process, as the material’s outer fibers are elongated to fit the new shape. If not accounted for, material stretching can lead to inaccuracies, resulting in parts that are too short or have improper angles.
Factors Affecting Sheet Metal Stretch
Several factors influence the amount of sheet metal stretch, including:
- Bend Radius: The radius of the bend influences how much the material stretches during the process. A smaller bend radius generally results in greater stretching of the material.
- Material Type and Thickness: The ductility and thickness of your fabrication material significantly affect how much it will stretch. For example, a more ductile material like aluminum will stretch more easily than a less ductile material like stainless steel. Additionally, thinner materials tend to stretch more than thicker ones.
- Bend Angle: The greater the bend angle, the more material is required to cover the length of the bend, thus affecting the sheet metal bend allowance.
Calculating Sheet Metal Bend Allowance
The general formula for calculating the bend allowance (also known as the developed length) in bending is:
BA = θ × R
Where: θ is the bend angle (in radians); and R is the bend radius (in inches).
Example Calculation:
If a part requires a 90-degree bend (which is 1.57 radians) and has a bend radius of 1 inch, the sheet metal bend allowance would be:
BA = 1.57 × 1 = 1.57 inches
This means that in order to compensate for material stretching, the length of the flat sheet must be increased by 1.57 inches to account for the stretch.
Accounting for Stretch in Forming & Drawing
In forming and drawing operations (such as deep drawing), material stretch becomes even more significant. During these processes, the material is pulled over a die, and the material at the edges experiences more significant elongation compared to the center.
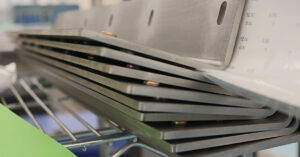
In deep drawing, this effect is especially pronounced, as the material must stretch to conform to the shape of the mold or die. The amount of stretch in such operations depends on the geometry of the part, the material properties, and the depth of the draw. For deep drawing operations, engineers use the blank diameter (the initial diameter of the sheet before drawing) and the depth of the draw to calculate the material stretching more precisely.
The basic formula for sheet metal bend allowance in a drawing operation is:
BA = Di − Df
Where: Di is the initial blank diameter; and Df is the final drawn diameter.
This formula helps to estimate how much the sheet metal material will stretch based on the difference in diameter before and after the drawing process.
Accurately calculating sheet metal bend allowance is essential for ensuring that sheet metal parts are fabricated with precise dimensions and functionality. Engineers must account for factors such as bend radius, material type, and thickness when calculating material stretch. Properly accounting for material stretch during bending, forming, and drawing is critical to maintaining the integrity of the part and optimizing the overall production process.
Machinery’s Handbook serves as a valuable resource for further understanding material behavior during bending. It provides formulas and guidelines that aid in the efficient and accurate design of parts. The book also includes detailed tables and charts that provide stretch allowance multipliers based on material type, thickness, and bend radius for quick reference when estimating how much material will stretch during bending.
If you’re seeking hands-on support in accurately determining the bend allowance for your custom sheet metal parts, look no further than the experts at PEKO. Submit your project details to our experts to receive tailored guidance that ensures your precision sheet metal fabrication projects are executed flawlessly.