Did you know that nearly 75% of all the elements on the periodic table are classified as metals? This vast array of options provides a diverse selection of fabrication materials for creating metal parts through cutting, welding, machining, forming, or assembling processes.
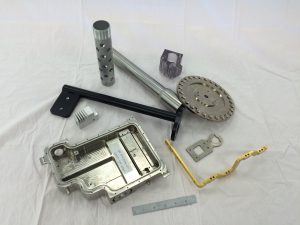
While virtually any metal or metal alloy can be utilized in the fabrication process, certain materials are more commonly used due to their distinct levels of strength, hardness, and corrosion resistance. Understanding the properties of different metals can help in selecting the most suitable material for your specific project requirements.
Here, we’ll discuss some of the more common types of fabrication materials.
Aluminum
Aluminum offers several benefits as a material type.
One of the biggest pros in fabrication is that it’s lightweight. Not only does this characteristic make it suitable for a wide range of applications, but it can also speed the fabrication process.
Another advantage of aluminum is that it’s a low-cost material option with a high resistance to rust.
Lastly, it has good formability since it’s softer than steel and easy to shape into custom designs. However, it’s important to note that this feature can also make it more prone to damage during fabrication, so you’ll want to work with a skilled fabrication shop.
Steel
That’s right, as in the various types of steels. First things first. All steels are alloys of iron and carbon. What differentiates the different types of steels are the additions of other materials. For example, the addition of at least 10.5% chromium is what produces stainless steel, while boosting the carbon content creates carbon steel. Let’s explore more below:
- Carbon Steel: Carbon steel refers to a low-to-high range of steel types differentiated by increasing levels of carbon. The ranges and ratios of carbon denoting each type is determined by the ironmaker. That’s why you may see three types of carbon steel at one foundry and four at another. Generally, however, carbon steel is broken down into the following categories: low, medium and high. Low (or mild) carbon steel is a versatile fabrication material that’s easy to cut and shape yet is still hard and durable. Medium carbon steel is harder and is typically formed or shaped before being treated to make it harder. High (or ultra-high) carbon steel is the toughest and most durable of the options, which is why you’ll often hear it referred to as tool steel.
- Stainless Steel: The primary advantage of this type of steel is in its superior corrosion resistance due to its high chromium content. If you’re planning to make a rust-free part or product, this material should be at the top of your list. It’s also resistant to extreme temperatures so can withstand heat well. From a fabrication perspective, stainless steel is moderate to work with whether you’re cutting, stamping or welding it. And for companies looking for a sustainable option, the material is 100% recyclable so it’s a good way to lessen your environmental impact. There is, however, a high initial cost when you choose to use stainless steel.
- Armor Plate: Armor plate is an air-hardening steel alloy that offers a good deal of protection. It’s fabricated in the forms of castings and rolled plates that are heat-treated to reach the desired level of structural and protective properties. As its name implies, the material can be found in a wide variety of military and defense applications such as in tanks and guns. One thing that can make armor plate challenging when fabricating is that it’s relatively heavy.
Brass
This metal alloy made of mostly of copper and zinc offers several advantages as a fabrication material. First, it’s less costly than pure copper, yet just as corrosion resistant, which makes it ideal for metal parts that need to be exposed to the elements. Second, brass has a high temperature tolerance, which is why you’ll see it used in applications like valves. Finally, brass is known for its machinability. Specifically, it’s easy to form and machine into even the most complex and detailed part, yet still retains its high strength.
Bronze
Bronze is another type of metal alloy, usually made from adding tin to copper to produce a fabrication material that’s harder than plain copper, and far more cost-effective. Advantages include its corrosion resistance, high thermal and electrical conductivity and a natural shine that lends itself to excellence surface finishes. Bronze’s advantages and versatility make it a common choice for products like hardware, architectural elements and safety tools since it’s non-sparking.
Nickel
Nickel alloys are known for their extreme resistance to corrosion and greater strength at high temperatures. These properties aren’t found in nickel itself, however, but through combining (alloying) the metal with other elements like copper, chromium, iron and molybdenum, resulting in a wide variety of alloys that are ideal for fabricating products needing to withstand severe conditions such as in marine applications, gas turbines and industrial furnaces.
Titanium
The main benefit of titanium is that it offers exceptional strength-to-weight ratios. Plus, it’s extremely corrosion resistant. These characteristics make titanium a good material choice when fabricating parts for the aerospace, marine, military and medical device manufacturing industries. However, a potential drawback of titanium is that it is more expensive than other metals. That means you’ll want to consider the amount of machining waste as you think about manufacturing a titanium part.
“Choosing the right fabrication equipment, feeds, speeds and processing methodology is paramount to manufacturing different materials” says Mark Frosino Engineering Manager.
As you can see, each type of fabrication material has its pros and cons and can provide different results. It’s important to carefully consider your project needs, budget, timeline, and other factors to choose the right metal material for optimal product performance.
Looking for a company to manufacture your metal part? Download our 8 questions to ask before selecting a sheet metal and welding fabricator to find the best metal fabrication partner or request a quote today.