In sheet metal fabrication, one of the most important considerations is ensuring the correct bend radius to prevent material failure and ensure the proper performance of parts. The bend radius is the inside radius of a bent sheet metal part and has a direct impact on the part’s structural integrity, its ability to withstand stresses, and its final quality. Incorrect bend radii can lead to issues such as cracking, poor fit, or material waste.
This blog provides comprehensive guidelines for determining the appropriate bend radius based on material properties, thickness, and bend angles, using Machinery’s Handbook (31st Edition) as the primary reference.
What is Sheet Metal Bend Radius?
The bend radius is defined as the distance from the inner surface of the sheet metal to the center of the bend. In simple terms, it is the radius at which a sheet metal part is bent to form a desired angle. The correct bend radius is critical because it dictates how much stress the material will experience during the bending process. When the radius is too small for the material’s thickness and properties, it can cause the material to crack, reducing the part’s functionality and possibly leading to failure under operational loads.
Key Factors in Determining Bend Radius
1. Material Type and Thickness
Different metals have varying properties when it comes to bending. Ductility, or a material’s ability to deform without cracking, plays a major role in how tight a bend can be without damaging the material.
For instance, metals like aluminum, which are more ductile, can often tolerate smaller bend radii, while materials like stainless steel or high-strength steel may require larger radii to prevent cracking.
Machinery’s Handbook (31st Edition) offers charts that specify the minimum recommended bend radii based on material type and thickness. For example:
- Mild Steel: K = 1.5 (bend radius is 1.5 times the material thickness)
- Aluminum: K = 2.0 (bend radius is 2.0 times the material thickness)
- Stainless Steel: K = 2.0 (bend radius is 2.0 times the material thickness)
The thickness of the material also affects the minimum bend radius. The general rule is that the thicker the material, the larger the required bend radius. Using a bend radius that is too tight relative to the material thickness can cause the metal to fracture, leading to a part that is both weak and potentially unusable.
2. Bend Angle
The bend angle also affects the choice of bend radius. As the bend angle increases, the material experiences more stress, and a larger radius may be required to avoid damage.
For example, bending angles that are acute (less than 30 degrees) tend to concentrate stress in localized areas, which can cause cracking if the bend radius is too small.
According to Machinery’s Handbook, bends over 90 degrees often need larger radii, and sharp bends (typically less than 30 degrees) should be avoided or corrected using special forming techniques like pre-heating or using softer materials.
3. Springback Considerations
After a sheet metal part is bent, the material has a tendency to “spring back” to its original shape. This happens because of the elastic properties of the metal. Springback is a critical factor that must be accounted for when determining the bend radius. The amount of springback can be influenced by material hardness, the bend radius itself, and the angle of the bend.
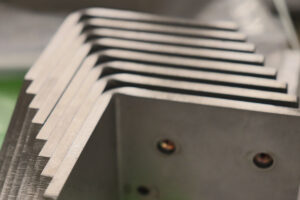
Machinery’s Handbook provides equations and guidelines for predicting springback, but it is important for engineers to consider this effect when planning the bend.
For example, after a part is bent to a certain angle, the radius may need to be slightly reduced during the design phase to compensate for the springback that occurs after forming.
Sheet Metal Bend Radius Practical Example
Consider a common scenario where a 1/8″ thick mild steel sheet is being bent. Using the guidelines from Machinery’s Handbook, the minimum recommended bend radius would be 1.5 times the thickness, or about 3/16″. For aluminum, which is more ductile, the bend radius could be 2.0 times the thickness, equating to 1/4″. Here’s a simple table summarizing the recommended bend radii for several common materials:
Material | K Value (Ratio) | Minimum Bend Radius (Inches) |
---|---|---|
Mild Steel | 1.5 | 3/16″ |
Aluminum | 2.0 | 1/4″ |
Stainless Steel | 2.0 | 1/4″ |
Copper | 1.5 | 3/16″ |
These values are only guidelines and may need adjustment based on the specific requirements of the part, such as the bend angle, forming method, or post-bending operations.
Properly determining the sheet metal bend radius is crucial for producing high-quality parts that meet both functional and aesthetic requirements. As outlined in Machinery’s Handbook, engineers must account for factors like material type, thickness, bend angle, and springback.
Understanding these principles is key to success in sheet metal design and manufacturing. By adhering to these guidelines and carefully considering the specific properties of the materials involved, engineers can avoid material failure, minimize waste, and optimize production efficiency.
Need assistance with your sheet metal design? Look no further than PEKO. With our expertise and experience in sheet metal fabrication, you can rest assured that your custom sheet metal parts will be executed with precision and excellence. Take the first step towards high-quality sheet metal parts by requesting a quote from our experts today.