I’ve said it before and I’ll say it again, we love working with hardware startups. When I try to put my finger on why, I’m not sure if I can. Maybe it’s because we love seeing new technologies in their infancy, or maybe it’s because we enjoy using 55 years of product development and contract manufacturing knowledge to give guidance to young and ambitious companies. But quite possibly, maybe we simply enjoy going along for the high-risk high-reward game that hardware startups are forced to play.
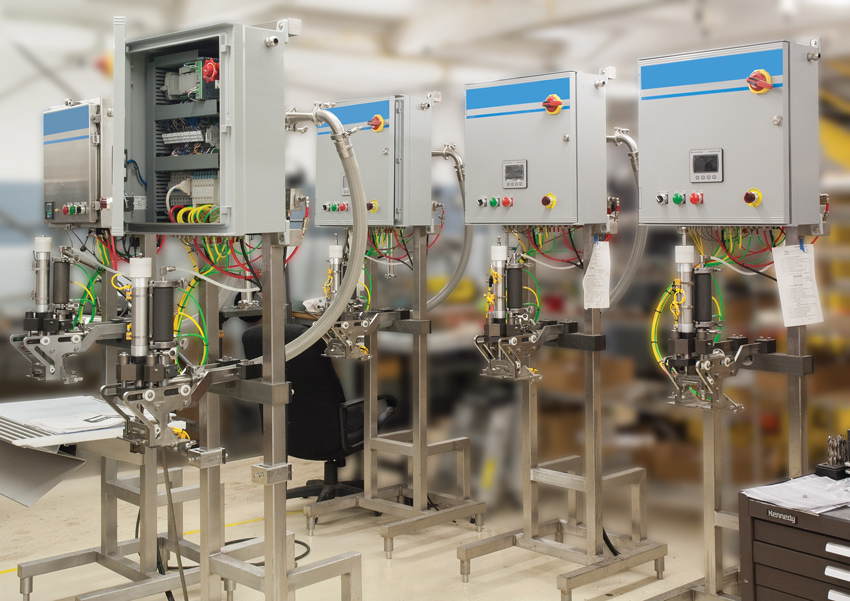
It’s a very challenging journey when a startup is working from a new product development prototype to scaling to mass production. In most cases, their core competency usually lies in the software and data management than the hardware itself. But most times, these companies will find themselves consumed with balancing engineering and manufacturing issues. These bottlenecks can range from constrained engineering resources and limited manufacturing capabilities to financial and investor pressures and finding real estate that’s a good fit for their business.
Regardless of the issues, startup management and the investors behind them are seeking large and quick returns on their investments, which means they need to go big. So today, we’ll look at some factors of what it takes to scale to mass production.
We’ll take a look at some common questions like…
- What is mass production?
- What must I have in place to scale up my hardware manufacturing?
- What are some common problems I will see along the way and how can they be avoided?
What is Mass Production?
According to Investopedia, mass production is “the manufacturing of large quantities of standardized products, often using assembly lines or automation technology.”
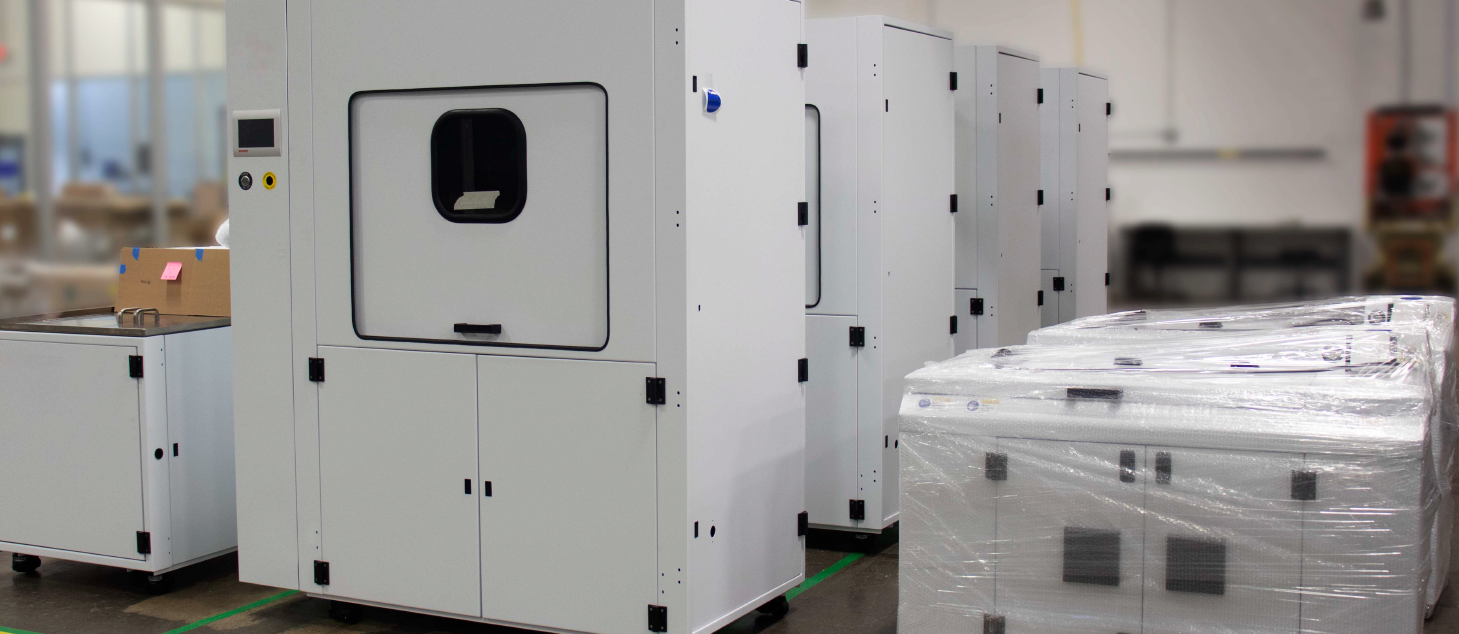
It’s the kind of thing that reminds you of automobiles, cell phones, and lawnmower manufacturing. It’s real and it’s impressive to witness. But the reality, especially for hardware startups, is that mass production looks very different than a factory costing hundreds of millions of dollars and many years to build.
Your mass production may be a manual or semi-automated cellular manufacturing layout with a few dozen assemblers moving hundreds or thousands of units through each year. Maybe the term “Full-Rate Production” is more appropriate in this case.
Of course, it depends on your product and market as well. A hardware startup selling hundreds of thousands of smart lockers will have a mass production vision that’s entirely different from a company that seeks to build a few hundred sophisticated 3D printing machines for a successful business model.
In any case, the paths and outcomes may look different, but the idea is the same. You want to get your hardware equipment to the desired production level to satisfy your investors and your business model and maximize the total available market share.
What Do I Need to Scale to Mass Production?
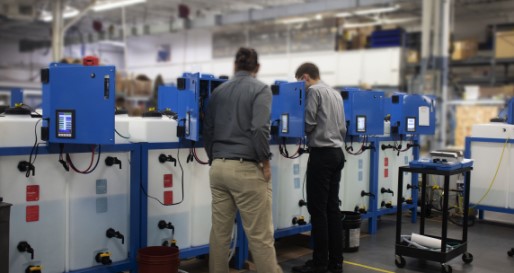
OK, so we’ve defined your end game… but let’s take one step back. What should you have in hand the day you say, “I’m ready to scale to mass production”? By this stage in the game, you’ve probably been working for at least a year on getting your equipment, machine, or other hardware new product development ready.
You may not have all this complete or perfect, but here’s a list of five things you should have in hand when the production handoff begins:
1. Bill of Materials (BOM)
A bill of materials (BOM) is a comprehensive list of parts, items, assemblies, and other materials required to create a product (as told by the product launch management experts at ArenaSolutions). Furthermore, an indented BOM has an intuitive tree structure that helps roll the parts into the subassemblies which then roll into a higher-level assembly (HLA). BOM management is important because both internal manufacturing and external contact manufacturing companies will use it for everything from supply chain management to rev control to assembly sequencing.
2. CAD Models
In all likelihood, your design team will have CAD models available at this point. CAD models are geometry files that detail and visualize aspects of your hardware, like size, shape, colors, materials, assembly, structure, and even simulations. There are many dozens of CAD drafting software available, with companies like Solidworks and AutoCAD leading the way. Internal and outsourced manufacturing will use these models as a guide during the builds to answer any questions that may not be represented clearly on the component drawings.
3. Detailed Drawings
Detailed drawings are the true manufacturing blueprints for the parts and sub-assemblies comprising your hardware product. Extra detail is given in these drawings, like material, tolerances, assembly notes, component notes, finishes, heat treats, quality specifications, and others. In most cases, detailed drawings take precedence over CAD models in terms of quality and manufacturing.
4. Technical or Engineering Point of Contact
During your transition to mass production, make sure to have a well-defined point of contact to handle the inevitable myriad of technical and engineering-related questions that will be flying back and forth between operations and the new product development team. Along with questions, there will be design recommendations and other considerations that will likely need to be addressed.
5. Manufacturing Business Case Analysis
Saved the biggest for last here. And with any luck, you’ve gotten this started well before your time to get your full-rate production started.
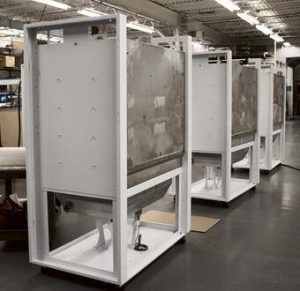
Your business case is going to be an extremely rigorous analysis of how you will actually conduct your mass production.
The parties involved will be managers from The New Product Team, CEO, Engineering, Operations, Supply Chain, Accounting, and more.
You’re going to be determining the who, what, when, where, and why of your mass production strategies. Key factors in this decision will be:
- What are the capital requirements and how will I fund it?
- Should I build my own internal manufacturing layout, hire a contract manufacturing company to perform the build, or perhaps a hybrid or insource and outsource?
- What is my production forecast? How does my scale-up curve look and how do I “right-size” my manufacturing to meet demand optimally?
- What is the timeline for production, and how to shorten it if needed?
- How do I handle excess inventory? What about inventory shortages?
- Who will negotiate the contract and how does it fit my business goals?
Common Problems To Expect Along the Way
Last year, I attended a conference, and a major executive from one of the world’s leading social media giants made a statement that I will never forget.
“There’s a lot of ways to offend people, but nothing makes them more irate than violating their expectations.
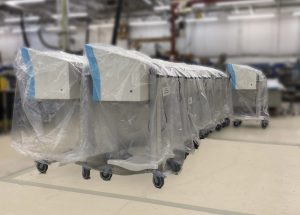
This quote, viewed through the lens of manufacturing, makes everything more clear. Quite frankly, you can take it to the bank. Mass production (and manufacturing in general) is anything but smooth sailing, so let me set some expectations for you.
Here’s a short list of common problems you’ll encounter along the way as you scale, and some ways to mitigate them.
- It’s far more expensive to prepare manufacturing facilities for mass production than you think. So you want to automate your plant? At a minimum, custom automation will cost you $100k per station, and then you’re stuck with it. A basic industrial robot is roughly $50k without any programming. Industrial workstations, lighting, and tooling are far more expensive than you’re used to at Lowe’s or Home Depot. What about real estate? Depending on the region, manufacturing floor space can be anywhere from $4 per square foot per month or $4 per square foot per year. The best way to get ahead of this is to do research on tooling, capital equipment, and real estate to understand what the costs really are so you don’t end up with sticker shock or blowing your whole business case.
- Someone will be late with something, and it will slow down your build. With a Bill of Materials of hundreds of parts sourced all over the world, you or your contract manufacturer will be at the mercy of dozens of suppliers. There will be quotes for prices and lead times. But I can assure you, something will happen to slow the build due to late parts. Maybe it will be a custom manufactured part. Maybe it will be a COTS ball screw with a long lead time. But when parts don’t land on the assembly floor when they’re supposed to, the manufacturing plan breaks down and the line comes to a very costly halt. Some ways around this are finding redundant suppliers, purchasing surplus parts, and designing in such a way that alternatives can be used in a pinch. You don’t know frustration until the day you’re notified that your long lead parts are going to take an extra month and you end up with a thousand units of your product in WIP (work in process) missing a custom e-stop button.
- Design changes, updates, and configuration. For good or for bad, your design might change during the mass production phase. What can change? Designs for custom fabricated parts, obsoleted off-the-shelf components, new and improved features, and more. This is normal, but it is not always easy to deal with. Internally, it is hard to set up a good configuration management process because frankly, it takes a lot of experience to track batches and serial numbers against all versions of the Bill of Materials. Externally, make sure you have a good contract manufacturing company that has this function built into its infrastructure.
Trust us when we say, the sky’s the limit when it comes to problems during mass production. Startups should be excited to get to mass production and take their business to its highest levels. Educating yourself and finding smart partners that will anticipate, mitigate, and react is really the key to success.
So, keep learning, keep pushing and you’ll be able to mass produce like a pro, set yourself apart from the competition, and make your investors very happy.
Contact us today to learn how PEKO can help your hardware startup with scaling to mass production.