Product Type: 3D Engineering Software
Manufacturer: SolidWorks
Model: We have varying seat levels. The different seat levels provide you with differing analysis levels.
Where to buy: Find a Reseller
Performance Rating: 4.5/5
Quality Rating: 4/5
User Friendly Rating: 5/5
Price Rating: 3/5
Overall Rating: 4.1/5
Introduction
At the turn of the century, 2D AutoCAD was dominating the 2D engineering software industry.
One of the most groundbreaking abilities the SolidWorks platform provided for our organization was the ability to export formats that can go directly to CNC programmers. While this methodology may seem as “common sense” in terms of manufacturing efficiency, at the onset of the 21st century this adaptive technology really paved the way for the digital age in factories. Today, most young engineers may not appreciate this ability of SolidWorks, yet those who have been with our company for a few decades can remember how this technology moved our business forward.
How Did PEKO Come About Using This Product?
Once the major software companies began to transition into the implementation of 3D, we had used, and still use, some of the other competitive platforms to SolidWorks. Since we were used to the AutoCAD platform in the land of 2D models, we initially implemented AutoCAD Inventor into our operation. Soon after we had SolidEdge, CREO and then finally SolidWorks. Today, most of the designs we work with are in SolidWorks, however it just depends on our customers’ preference.
Since we are a Contract Manufacturing Organization, the designs we work on are the SOLE property of our customers, not PEKO. When we work on a customer’s designs, our goal is to make sure that it looks like the customer designed the product themselves–we do not, nor do we want to, own any design. Because of this, we not only carry all of the major engineering software platforms, but we carry all of the platform’s latest versions, along with several of their outdated versions. We need to know that our customers can open the files we send to them, so it’s necessary for us to have multiple programs to make their transition into and out of our organization as seamless as possible.
What Are Some Benefits We Have Seen?
- 3D Design–easier to see interfaces
- Quicker concepts drawn than with 2D
- SolidWorks is far more intuitive than its competitor Creo (less strict on ways you can assembly “more flexible” and forgiving)
- The Simulation Analyses the software offers has allowed us to perfect parts within our machines prior to mass producing machines.
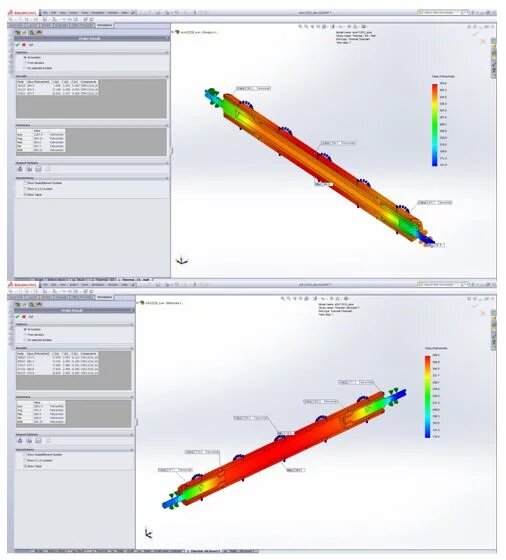
What Are Some Shortfalls of This Software?
- Software bugs and crashes (updates are set to the subscription-based services in order to handle and update these issues)
- Since we are a Contract Manufacturing Business that serves our customer base, we have to maintain the last 5 years of SolidWorks versions to make sure that our customers can open the files we send to them. However, this “shortfall” is very specific to our organization and if you were thinking of implementing the software into your business, unless you had a similar operation to the way PEKO works, you should be fine.
- Current versions only offer a subscription model which can be expensive depending on the number of seats needed.
Price vs Value
There’s no way around it: SolidWorks is an expensive subscription-based platform. However, the product itself is a great tool to get an engineer’s ideas out and onto “paper.” This software isn’t going to design anything for you, an engineer still needs the creativity to design their solutions, however SolidWorks is still a great tool due to the simulation analyses provided with higher seats.
Compared to its competitors, SolidWorks is far more intuitive. When putting together a model, if you want to delete a step in a deigns process you can–which is something that is not allowed in other programs unless you want to redo each step following thereafter.
How Well Does It Work and How Is the Usability?
In today’s world, almost every engineer is either trained on a similar 3D CAD software or has been actually trained on SolidWorks. In either case, in this digital tech-savvy age, our co-op engineering students are well versed in implementing SolidWorks into their flow. If they know one platform, it’s easy for young engineers to transition into another 3D CAD program.
Back in the day when SolidWorks first came out, some of our older engineers took a bit more time to understand the platform due to a steep learning curve. Although, much of their issues corresponded with the technology gap that is not seen in the youth of today. Most of our younger engineers, and those who are here for co-ops, have either used SolidWorks prior, or have used a similar platform so they have no issues learning the software.
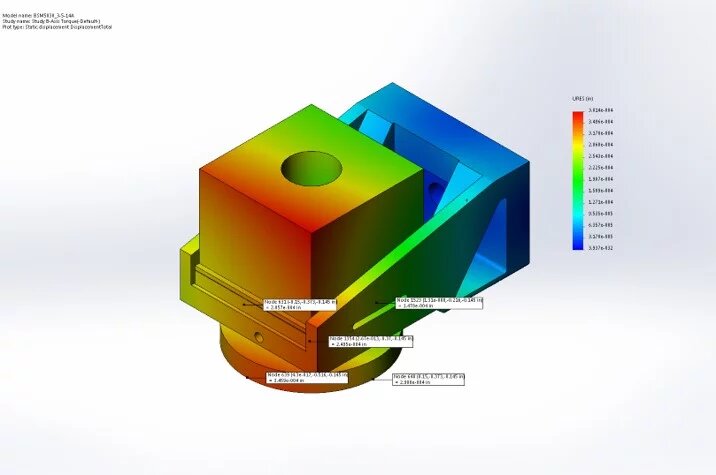
What Were Some Alternatives We Could Have Pursued?
Again, there are a few well-known competitors to SolidWorks when it comes to 3D CAD software and we actually carry all of them. Since we have a very specific business model that caters to our customers and the programs they use, we have to have access to their preference as well as the past few versions of each platform. Overall, if it were up to us our first choice would be SolidWorks.