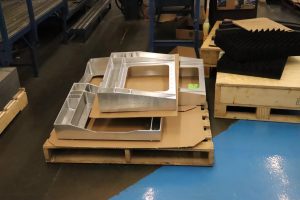
We all talk about robotics, but our experience tells us that your typical small shop or those with a high mix/low volume production environments can be adverse to such technology. Common rebuttals for pursuing robotic automation in high mix machine shops are “it will take too long to setup” or “it will be too expensive”.
This article identifies such objections:
“Mr. Oreskovic believes some robotic machine-tending solutions can be intimidating to small job shops. This can cause them to delay their transition to automated manufacturing because they think they need to invest in complex, expensive, process-specific systems that rely on highly trained specialists.”
Dive deeper and you see how a process is laid out the subject overcame such obstacles, like starting small. We agreed with this take and thought it very wise.
The article explains how this strategy can be implemented in high-wage companies, a theme in which most western companies can sympathize. The discussion on quick-change workholding as a means for improving setups was right on point. Carefully selecting grippers compatible with common work geometries or part families is exactly the kind of smart thinking that many shops could analyze before spending a single dollar on robotics.
Stage two and three of the process laid out in this piece, are Robotic Loading for Pallet Pools and Vice clamped parts. Our gut reaction is that this sounds difficult to optimize, however I agree that by focusing hard on efficiency gains and using creative methodologies, there could be gold in those hills. I applaud the author and the subject both for vetting out the process.
The article closes the loop and informs the reader that such an investment has paid off. As we look to the future of robotic automation, I ask, how can other machine shops use a similar process? What kind of human capital is involved in successful implementation? What’s taking so long for high mix/low volume shops to adopt such a process? What are some process limitations? And lastly, are these systems flexible enough to account for changes in future business demands?
The full article, Small Shop Sees Big Gains from Right-Sized Automation, was published on Modern Machine Shop. Thanks for checking out this PEKO Perspective.
Check out some of our other PEKO Perspective articles below: