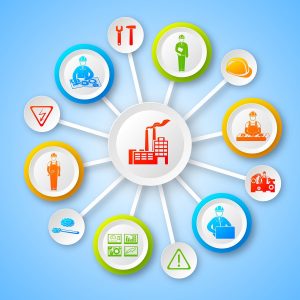
Whenever I visit a low-volume manufacturing facility, I notice a common theme. Folks that are building things like medical equipment, industrial machinery, and lab instrumentation are usually fighting a battle trying to coordinate dozens if not hundreds of vendors.
To add insult to injury, this coordination extends into the manufacturing schedule and marketing forecast. All it takes is a few suppliers not to perform and the whole build stops. We’ve seen it over and over again.
While there are many bandages, there are few true solutions to these inevitable pitfalls. One of the most effective ways that OEMs are able to combat their outsourcing woes is to outsource manufacturing to companies that can add a significant amount of value before it gets to their floor. This usually comes in the form of assemblies.
Below, I’ll outline the 3 low-hanging fruit areas that OEMs can save money by outsourcing assembly manufacturing.
1. Internal vs External Labor Costs
Most Fortune 1000 companies carry huge burden rates, easily over $150/hr. By hiring a good contract manufacturer to take over a portion of the work, those value-added hours can translate to big savings. Those savings alone may be 50% or more on value-added. Overall companies could see a 10-30% reduction in costs simply by utilizing vertically integrated suppliers that can do the component work and then the assembly work. It’s simple algebra but it is a commonly overlooked way to source because finding the right suppliers is relatively difficult.
2. Avoidance of Extra Markup, Shipping, and Handling Costs
Besides the labor rate, an added bonus of outsourcing assemblies is that there are big savings in vertical integration. A contract manufacturer that has internal capabilities of CNC machining, sheet metal fabrication, wiring, welding, assembly, and more can avoid the markup that is typically tacked on by using a variety of suppliers in the chain. Saving on the markup of multiple suppliers combined with the extra savings of avoiding big shipping and handling costs is an easy way to realize quick and easy cost savings!
3. Minimize Overhead Costs
Lastly, effectively outsourcing assembly manufacturing will help decrease some overhead costs. These costs can be somewhat hidden since they are not usually factored into the build price internally. Certain supervisors, supply chain managers, inspection personnel, and even maintenance folks can all be reallocated so that their time is used more effectively. If you’ve ever met a supply chain manager that has to manage 50 suppliers for 250 different parts, you know what I’m talking about. Productivity and morale should certainly increase.
These are just three low-hanging fruit ways to help save money by outsourcing assemblies wisely.
Taking advantage of burden disparities, eliminating markup from the supply chain, and relieving the burden of overhead employees are all easy ways that a contract manufacturer of assemblies can contribute to your bottom line and time to market.
For more information on how PEKO can provide contract manufacturing for your outsourcing project, submit your project details and one of our engineers will get in touch with you.
Share article: