All across the United States, Medical OEMs are looking for a pool of competent medical device contract manufacturing suppliers to help in the manufacturing of their medical devices. Medical devices require a different level of manufacturing process documentation and traceability than do their counterparts in less regulated industries. This level of sophistication requires Medical OEMs to choose a supply chain that can also adhere to these strict requirements.
The ISO 13485 standard is a very good way OEMs can initially assess whether a supplier has a quality system even capable of dealing with the requirements. In plain English, the ISO 13485 directs companies to do things like establish/document a quality system for medical devices, create management requirements, and identify resource requirements.
Suppliers in machining, sheet metal fabrication, contract assembly and other areas still must prove that these systems are in place when applying for their ISO 13485 certification. Suppliers like these have validated process control that account for value added quality methods. Medical device contract manufacturing with CNC machining, sheet metal, and assembly is certainly a difficult animal. Suppliers in this category are much different from the mom-and-pop shops with quick turnaround and a few machines.
First Article Inspection Processes
CNC machine shops and fabricators must do a First Article Inspection (FAI) on all products that fall under the ISO 13485 requirement. The purpose of the first article inspection is to provide an objective system that ensures all design and spec requirements are accounted for, verified, and documented. When the processes are finalized and under control, the FAI is the verification. Maintaining a system like this is complex and expensive. The management team from the top down must maintain the discipline and commitment to ensure the system is managed and followed correctly.
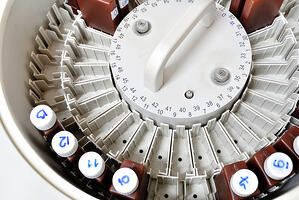
Experience in the Medical Industry
OEMs use contract manufacturers for a variety of reasons – price, delivery, resource optimization. When searching for a medical device contract manufacturer, another thing companies are looking at is experience. With devices such as blood analyzers, DNA sequencing systems, clinical chemistry equipment, mass spectrometry, and more, it is important that the company is familiar with the technology and all the facets that make a quality product. By having experience with multiple players in this industry, a company can prove they have the capabilities and processes to manufacture sub-assemblies or products in this field. This demonstration of success is an important part of supplier selection.
Robust Traceability Systems
A good ISO 13485 medical device contract manufacturer is going to have a robust system that accounts for the identification, traceability, and status of the medical device. These should dovetail into the OEM’s system nicely. Creating a maintaining a system like this is no easy task. Requirements cover parts of the organization like, raw materials, components, materials used for the production, lots or batches, finished goods, defective, or returned goods. Along with the preceding these, the customer and regulatory requirements are very specific and require investigation from a seasoned quality team.
Medical OEMs and Medical Device Contract Manufacturers can work together to save time, money and resources while maintaining the level of quality and traceability required by the ISO 13485 standard. Some components of this partnership are first article inspection processes, traceability systems, and a long history of experience in the industry. Companies like PEKO have years of experience in this kind of Medical Device Contract Manufacturing. For more information or questions, contact us using the form below.