One of the most fun things about being part of equipment manufacturing company is getting all the industry news every day.
Everyday my inbox is full of news about the latest technologies and how they are being implemented successfully into the latest equipment and products.
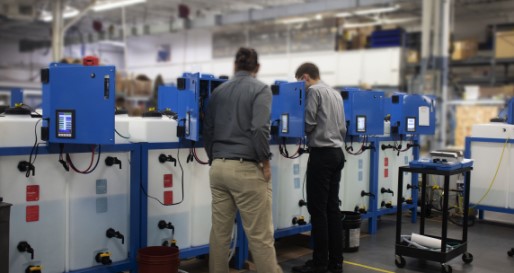
Without a doubt, a lot of these are ads and other kinds of paid content. But who cares? It is very interesting to see our peers pushing the bounds of manufacturing and sharing their findings.
Manufacturing can be a tough road, and some balance of secret sauce and publicly shared information can be a really good thing. News feeds, videos, paid content, and other sources are excellent forums for companies and industry experts to show and tell the coolest, most exciting applications that are being used in their fields.
Today I’ll talk about a few of the interesting ones I’ve seen lately, and you can judge whether they might work for you.
Additive Manufacturing
Additive manufacturing applications have absolutely exploded in the past 10 years. In the world of equipment manufacturing, 3D printing has had numerous impacts in…
- The way we design parts
- The types of parts and materials that can be printed
- New cost benefit analysis techniques compared to casting, CNC machining and others
Tradeoffs between manufacturing cycle times, part tolerances, material types and capital equipment expenditures are all taken into consideration. And not to mention the post processing techniques that come along with additive manufacturing.
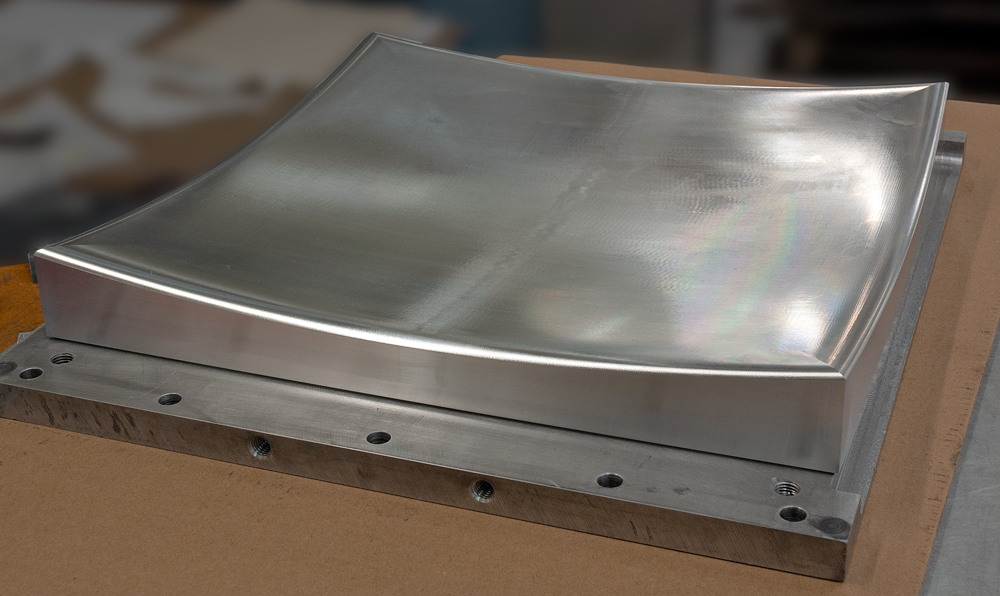
All things considered; additive manufacturing has created a new process type that has many exciting advantages in the right application. Historically, there has been hesitancy in high-volume production manufacturing with additive manufacturing. One of the major problems is that with most parts, the high volumes combined with long cycle times are a barrier to production, causing these parts to be better candidates for tooled up CNC machining, molding or casting processes.
While this is still the case, companies like Cummins are learning how to use binder jet technology to produce critical components at production volumes. In an Industry Week article, we learn that about how they are using binder jets for a critical engine emissions component.
“The part, now moving through Cummins’ production part approval process (PPAP) for formal approval, is a Cummins Emission Solutions (CES) lance tip adapter used in high horsepower engines.”
With the likely success of this part run, Cummins will enjoy the benefits of lower costs, increased speeds, improved functional geometry, and elimination of complex manufacturing operations. Our engineers at PEKO have been designing and producing similar equipment for one of the top 3D printing equipment manufacturing OEMs and have seen similar results on internal part runs. These are very exciting times.
Robotics
Robotics are the past, present and future of manufacturing. This month, I plan on writing another blog highlighting the new collaborative robot, or Cobots, that are permeating the market as we speak. But I’m no prophet, industry has been touting this technology very loudly in the past few years and this year is no different.

New robot applications are being discovered every day and following these new advancements has been very fun. One of my favorite news sources, Industry Week, ran a great article about the city of Pittsburgh and the budding robotics technologies coming from the area. We are all aware of the Tech hub of Silicon Valley, and the Innovations in Renewables and Medical from the Boston Area, but now it looks as if Pittsburgh is making a name for itself as the center for Robotics Manufacturing.
Traditionally, we’ve pictured robots building vehicles on automotive assembly lines at high speeds. More recently, companies are using robotics for cool new application. Portable inspection equipment, autonomous vehicles, space exploration, and security systems are all part of the mix. Right now, PEKO is working with some very innovative equipment manufacturing programs for automated material handling systems, which is a fast-growing sector as well.
3D Virtual Tours
Equipment manufacturing relationships are a B2B industry that largely revolve around face-to-face meetings. For instance, during the early stages of a contract manufacturing relationship, it’s extremely common for the OEM customer to visit the factory where the equipment manufacturing takes place. They want to be able to envision their product in the facility, view the flow, check for cleanliness and size.
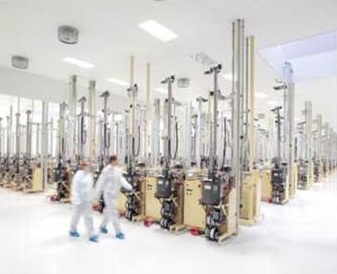
Recently, business travel for these endeavors has slowed dramatically due to the COVID-19 pandemic. Combine that with the internet bringing more and more companies together during the vetting process, and you see that there is a demand to show more of your factory to interested parties.
Enter the 3D virtual tour. A 3D virtual tour is a fully immersive experience where a user can freely, or with predetermined navigation, move throughout a factory and is definitely a notable equipment manufacturing trend. The user can see machinery, equipment, space, size, lighting and just about any detail. These tours have the navigation experience of Google Street view, but with incredible definition. It is as close to really being there as you could imagine.
The benefits are increased visibility, supplier credibility, and ease of use. The downsides we’ve seen are cost, time to create (we captured about 60,000 square feet over the weekend), and security (make sure you protect your links). Matterport is an up-and-coming host for this service and has local agents across the country.
Trends in equipment manufacturing can range anywhere from capital equipment to new industry segments to new ways to promote products.
The exciting thing is that the manufacturing industry is more open minded than ever about trying new things and using advancements in engineering, communications, hardware and software to enhance their offerings.
For more information on how to find an equipment manufacturing partner, download our guide to outsourcing to a contract manufacturer and self-assessment checklist for evaluating who will be the best partner for your project.