Designing and building machinery and equipment in a contract manufacturing environment is tough! To do it right, and at scale, you need a team of well qualified professionals to help the process go smoothly.
These folks each have unique roles and responsibilities that, when combined, are the recipe for successful machinery and equipment contract manufacturing. Today, we will talk all about engineering, program management, supply chain management, and operations management, all crucial roles in equipment manufacturing.
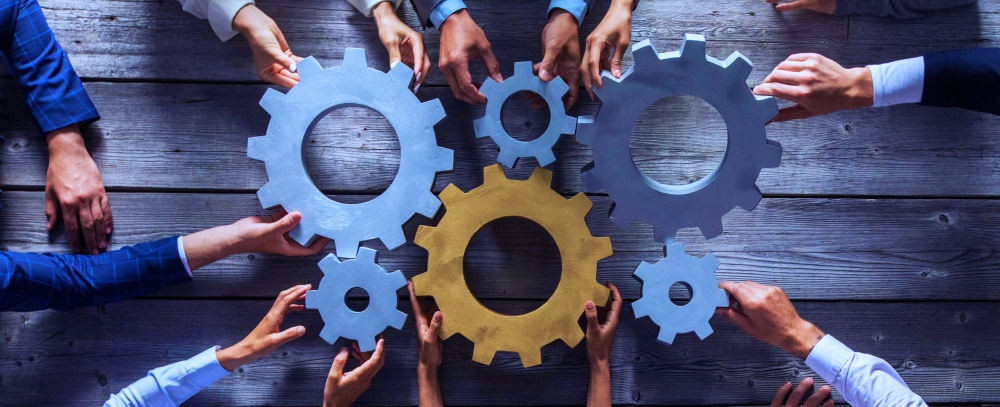
1. Engineering Experts
The engineers play one of the most important technical roles in equipment manufacturing and design. For most machine builders, it’s common to have at least one, if not all, of the following types of engineers on your equipment manufacturing team:
Mechanical engineer
- Electrical/controls engineer
- Test engineer
- Manufacturing engineer
- Software engineer
Most people think that engineers spend all day designing on CAD, but in reality, the engineering team takes on several crucial roles in equipment manufacturing. The engineers on the team are tasked with coming up with alternative designs, optimization techniques, component substitutions, DFMEA, among a host of other important tasks. Beyond this, engineers in equipment manufacturing will also step away from their desks quite often to get their hands dirty on the machines they’ve designed.
Early stages of the build or product lifecycle typically have more engineer personnel tending to the equipment. Problems in design, manufacturing, assembly, and electrical integration are very likely to show their head in these early stages. The engineering team is responsible for finding the root cause of these problems and coming up with a viable solution. Ultimately, the engineers are responsible for the design, functionality, and physical parameters of the machine.
2. Program Managers
The program manager is a major stakeholder in the success of a new product introduction or continuing equipment manufacturing program, and thereby plays a crucial role in equipment manufacturing teams. He or she is usually a seasoned veteran in the field and is responsible for deliverables and key success metrics, like cost, quality, and delivery.
The value of a program manager is that they have the experience to foresee problems before they arise and to successfully deal with inevitable problems. In addition, it is not uncommon to see the program manager picking up the slack for their team, whether that’s calling vendors to get parts on time, chasing down internal documentation or handling a quality crisis.
Think of your program manager as the general contractor for your project. Program management serve as the bridge between the customer and the machine building team, coordinating with all parties involved and connecting directly with the customer to ensure proper communication so that there are no interruptions to schedule or cost.
For best success, the program manager is usually assigned their role early in the program, so that they can build familiarity with the machinery product and the machine building team involved.
3. Supply Chain Managers
Equipment manufacturing usually takes dozens, if not hundreds, of outside and internal vendors to properly integrate the systems. This is where supply chain management comes into play, another critical role in equipment manufacturing.
The supply chain manager is tasked with coordinating huge databases of potential vendors that are vetted for specific processes in the equipment manufacturing lifecycle. A good supply chain manager will have the knowledge to match the engineering requisitions to the right vendors. In doing so, a list of vendors for each commodity can be created for quotation to find best price, quality, and delivery. This is no small task, so the supply chain manager usually has buyers and purchasing agents on their team to help with the details.
Supply chain managers remain pretty closely involved through the entirety of the project because they are not only monitoring what needs to be ordered, but also the status on what has been ordered. Without supply chain managers in the loop, ordering the right parts from the right supplier would be extremely hard for the engineering team to manage.
4. Operations Managers
Last, but not least, the operations manager is another key equipment manufacturing role and are often tasked with things like throughput and facilities layout.
In many cases, operations managers start off as engineers. They utilize lean six sigma techniques to ensure the success of your machine build and are obsessed with overall throughput and quality.
Operations managers may oversee a single build or an entire equipment manufacturing plant. You can find them constantly walking around the plant, reviewing the statuses on their plans for efficiencies, throughput, and bottlenecks.
As you can see, building the right team to build machines does not happen overnight. These equipment manufacturing roles are crucial to the success of a machine building team. Their functions have a lot of depth that require a long time to cultivate.
If you’ve got some new machinery that you need built, use our guide to choosing a machinery and equipment contract manufacturer to help you decide on the best pick for your business.