If you’re looking for contract manufacturing of machinery or equipment, you’ll find that you have a lot of options. You’ll also find that the services offered at machine shops will typically overlap and that the terms they use to define themselves are confusing and vague, such as ‘traditional machine shops’, ‘precision machine shops’, ‘CNC machine shops’, ‘conventional machine shops’, and ‘custom machine shops’.
This can cause uncertainty amongst strategic sourcing personnel, who are tasked with finding the contract manufacturer who offers all the services required to complete your project. Disregarding all this other industry jargon, there’s really one key distinction you need to make in your search for the right machine shop: the difference between a custom machine shop and a conventional machine shop.
What is a Machine Shop?
Before we get into the differences between conventional and custom machine shops, let’s start with the basics: the definition of a machine shop. According to Merriam-Webster, a machine shop is a workshop in which work is machined to size and assembled. That’s a pretty broad definition so we’ll get into a little more detail here.
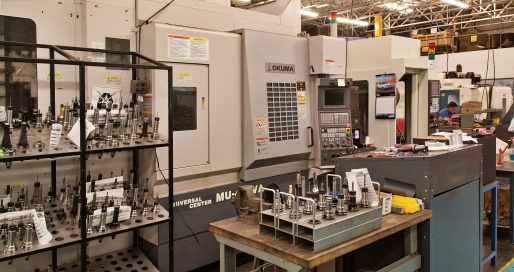
Advanced CNC Machinery and Workholding Tools.
A recent article described machine shops as the supporting actors of the manufacturing world. Essentially, they take raw materials and form and finish them into parts for use in another machine or product. The raw materials can be anything from common metals like aluminum, brass and copper to foam and plastic. To shape these materials into a final part, the shops use a variety of tools, including:
- Drill presses
- Saws
- Grinders
- Sanders
- Milling machines
- Lathes
Sometimes these machines are controlled manually, however, robots and computer numerical control (CNC) machines are increasingly in control of the operations, and that’s one of the fundamental differences between conventional and custom machine shops.
Conventional Machine Shops
In conventional machine shops, which is used interchangeably with the term traditional machine shop, a machinist operates using a number of the machining tools that we just discussed in order to achieve a desired outcome. This requires that there be a skilled technician in the shop for every machine.
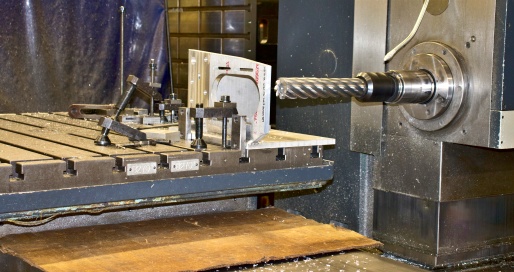
Close up of CNC bore milling machine.
Some potential downsides of relying on manual operators are:
- Reduced accuracy: Since the operations of manual machines are controlled by a human, there is a potential for error.
- Safety risks: With manually operated machines, operators are close to the sharp cutting tools, putting them at risk of an injury.
- More labor: A manual machine requires both a skilled operator for each machine and a supervisor, increasing your labor demands and costs.
- Less customization: For jobs that require several cuts with detailed customization, it can be next to impossible to create these complex shapes manually.
- Lower production rate: A manually operated machine only runs when a machinist is working, while CNC machining can be programmed to run 24 hours a day.
So why would some companies choose to partner with a conventional machine shop? The most obvious reasons are cost and production quantity. CNC machining operations used in custom machine shops are not as cost-effective for small projects, so if you have a one-off need, a manual machine shop may be the better option for you.
Custom Machine Shops
A custom machine shop is a machine shop which uses cutting-edge technology and equipment like advanced CNC machine tools to best serve its customers. By leveraging modern machines, they’re able to offer enhanced fabrication processes, which is particularly important for parts with special requirements, like those used in the renewable energy industry.
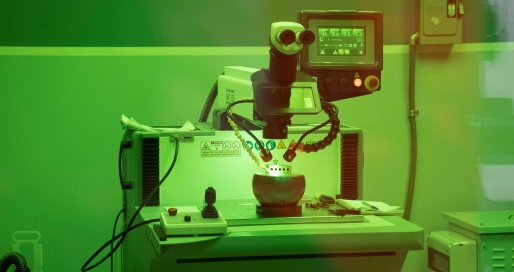
PEKO has advanced CNC machining equipment and manufacturing capabilities, including laser welding.
Custom machine shops that offer advanced CNC machining services, like PEKO, can manufacture hard-to-make parts such as those with:
- Difficult geometric tolerances
- Strict quality requirements
- Large overall dimensions
- Tight process control
And they can execute these demanding tasks every time. Repetitive uniform production is the main advantage of CNC machining.
Other benefits of this approach include:
- Precision: Using software, rather than humans, to cut parts can achieve greater accuracy, normally within 1/1000th of an inch.
- Greater flexibility: In addition to standard technologies, some novel machining equipment, like lasers and water jets, as well as special features and tool accessories offer more flexibility when it comes to fabricating a part.
- More capability: With the use of CNC machines, you’ll realize greater production outputs that can’t be reproduced using manual machines.
- Reliability: Instead of depending on operators to run the machines, CNC machines can run round the clock and only have downtime for repair or maintenance.
Does this sound like the right fit for you? By partnering with a custom contract manufacturer of machinery or equipment, you’ll benefit from a shop that offers a made-to-order approach with the right equipment and tools that can be invaluable to your final product.
According to PEKO’s Quality Manager, Jeremy Turcott, “Managing our machine shop has paved the way for our evolution as a contract manufacturing business.”
Looking for a custom machine shop capable of producing your complex parts and assemblies? Download our guide to finding the right partner to satisfy your custom machining needs today.