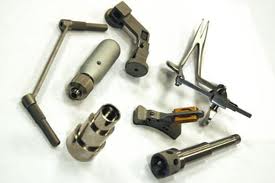
You have developed a technology that you believe can be a viable electro-mechanical device. But for right now, you only have a lab or benchtop concept, and you will eventually need to present your idea and get investors interested so you can start some fundraising rounds to go forward.
So where do you go from here? Well, as we are all aware, nothing speaks to people like being able to physically hold something in their hand. This means you’re probably going to need to build a prototype.
Our number one tip for building a prototype of your technology:
The more of the basic technology functionality you can show off in the prototype, the more receptive your audience is to it. It shows that the idea is more than a dream and more than a good lab experiment and being able to hold it and connect to it can make all the difference.
But how should you build a prototype?
These days many people ask us, “do you offer prototype 3D printing?” Our answer: No, we do not. So why is this?
As a well-versed contract manufacturer of complex machinery and electro-mechanical equipment, we have found that building a prototype can be done cheaper, faster, and with better functionality when done using other manufacturing processes.
While 3D printers are a good and improving technology, what many people don’t realize is that, in many cases, a modern manufacturer can machine what you need for your prototype in less time and at a lower cost than what 3D printing a prototype can. That’s right: faster and less expensive.
Also, consider functionality. 3D printing prototype components often will not be able to provide structural integrity, especially when produced with a stereolithography process, which will be needed to display the function of moving parts. Even on smaller load-bearing components, the print process can leave a layered and rough surface for mating parts that make operations uneven and noisy.
Does 3D printing have a place in building prototypes? Sure does, but so does more traditional manufacturing, and you may be surprised what can be done in a modern facility. So don’t lock yourself into a process path at first but engage a manufacturing partner that can provide you with cost-effective solutions.
At PEKO, our engineering team will take the time to understand your products. Our model shop can produce prototype parts in 3-14 days, and our production team has 85 CNC machines ready to move your product into higher volumes. Contact us today to learn more.
For additional guidance on choosing an ideal engineering and manufacturing partner for your prototyping project, download our new product development self-assessment guide, which is specially crafted for the likes of hardware startups and new product teams. Whether you need design, development, or full blow contract manufacturing, this guide will help you self-reflect.