Machinery manufacturing can be done in the back lab of your headquarters or in a highly sophisticated manufacturing plant. Every capital equipment or machinery manufacturing project has a different flavor.
Some call for a one-off machine to perform some automated operation. Other initiatives revolve around a complete product launch and commercialization effort to bring an entire machinery line to market.
There are about a hundred different trajectories between the two. Boston Consulting Group estimates that the industrial machinery industry is roughly a $2.5T sector, yet you probably don’t get into this kind of discussion with your in-laws at Thanksgiving dinner.
The knowledge and intricacies of this sector are largely kept within industry professionals. We think it’s time to bring our knowledge on the subject out in the open. New and exciting machinery industry segments are popping up all over, and the fundamentals of machinery manufacturing that are laid out below will help innovators, new and old.
So, whether you’re in the 3D printing, smart vending, or robotics industry, these pillars will apply to you.
1. Bill of Materials (BOM)
A bill of material (sometimes called an indented bill of materials) is an organized listing of all the subassemblies, components, and other parts associated with a piece of machinery or equipment. The BOM is referenced both during manufacture and at the time of service. You will find most bills of materials in table or excel format for ease of sorting and filtering. The columns include items like part numbers, descriptions, part revisions, the number of parts per level, supplier information (sometimes including prices), and notes.
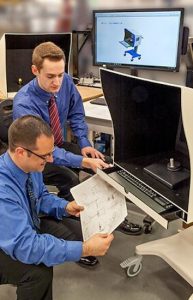
Most of today’s CAD software will generate an organized bill of material directly from a model. The formatting generated by the CAD software may need to be updated with pricing or other columns to be useful to all parties. In some cases, there are ways to customize the outputs so that the CAD software, bill of materials, and ERP can easily synchronize.
Your BOM is extremely important because it holds all the ingredients and organization that make up the machinery, equipment, or product. Some challenges we see often are BOMs that are not complete, not accurate for sourcing, or not up to date with the latest revisions. All these problems can cause major issues when it comes time to build the machine.
In some companies, there are specialists or configuration control managers whose main role is to ensure BOMs are accurate and up to date. For example, when a new customer arrives at PEKO, we are fully prepared with a team of engineering and manufacturing experts that can assist in finalizing your bill of materials to get it where it needs to be in order to be successful. Regardless of whether you’re using a machinery contract manufacturing company or an internal supplier to build your machine or equipment, an accurate bill of material is going to drive short and long-term success for the builds.
2. Models & Prints
While the BOM is the listing of ingredients to build the complete machine, the CAD models and prints are other pieces of documentation that serve as the blueprints of the machine at a much more granular level.
CAD models (or models for short) are computer-generated versions of the entire machine, the sub-assemblies contained within, and even the component-level parts. The models are typically 3D, which makes them fairly easy for humans to understand, view, and assess. Today’s modeling software can generate extremely lifelike visualizations and even simulation capabilities that have helped revolutionize machinery manufacturing as we know it. Gone are the days of pencils, erasers, and drafting rooms.
The simulation’s features are incredible for building industrial machinery that is intended to perform operations. One can test different methodologies for cycle times, fitments, and other performance criteria. There are also mechanical analysis capabilities like deflection, stress, pressure, and hundreds more. The flexibility, speed, and enormous array of analysis capabilities provided by CAD models are absolutely critical for today’s machine manufacturing and engineering teams.
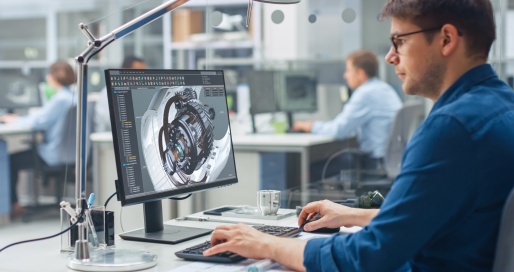
Prints (also called detail drawings) are a 2D interpretation of the models with more notes, specifications, and acceptance information. During the manufacturing processes, the manufactured components or assemblies must match the dimensions, tolerances, and notes that are specified on the drawings. In most cases, especially in the case of discrepancy, the drawings take precedence over the models. Each item on the BOM will have a corresponding drawing with matching rev. Keeping all of these in sync with the latest version is a difficult task, but critical to ensuring proper manufacturing.
Detailed drawings are usually created by an engineer of the associated discipline. One huge discrepancy we see in the industrial machinery industry is that mechanical engineers often are not trained to design parts and assemblies with manufacturability in mind (called DFM or design for manufacturability). Tolerances that are too tight, assembly features that are inefficient, and specifications that are over or under-designed are all common issues we see.
A good contract machinery manufacturing company will give you constructive feedback on this at the time of quote, and certainly at the prototype phase. At PEKO, our engineers are consistently working to improve a project’s DFM in order to optimize designs, reduce overall costs, improve efficiencies, and ensure the long-term success of each project.
3. Sourcing
When it comes to machinery manufacturing, sourcing is another huge issue. With a BOM laid out and your design completed, procurement will then need to source all the parts. There’s always a combination of custom-fabricated parts and COTS items.
Custom fabricated parts can be anything to the tune of machined parts, sheet metal components, frames, rollers, bearings, plastic molded parts, and more. One best practice is to reduce the number of custom components, as they can be a huge driver in cost. Another strategy for sourcing these parts is to get quotes from a handful of different suppliers for each category.
Depending on the vendors’ capabilities, workload, and lead time, you may get a huge disparity in pricing in any given category. You need to identify the best mix of price, reliability and lead time for each. This is a very time-consuming process, and it helps to leverage previous relationships. We’ve written about places to find manufacturers as a helpful guide for those searching.
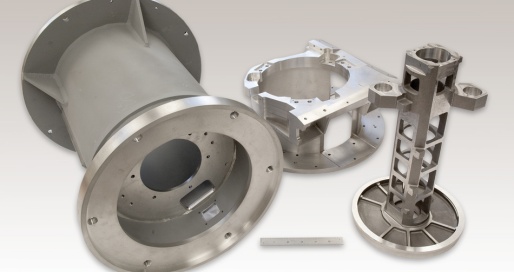
The other issue is commercial-off-the-shelf (COTS) items. Some common examples of COTS in the machinery manufacturing world are Servo Drives, Motors, PLCs, Power Supplies, Rails, Slides, and more. Really good machinery designs have already specified easy-to-find and readily available components. Most industrial OEMs will be sourcing from a combination of manufacturer reps (who are probably calling on you weekly basis), catalogs like Grainger or McMaster-Carr, and local/regional distributors.
Oftentimes, the BOM includes the supplier and/or manufacturer for each part. In sophisticated systems, this is all synced into an ERP for order placement. Depending on the economy, COTS should be relatively easy-to-find with reasonable lead times. In the cases where they aren’t, your engineering team should be able to provide alternates. If sourcing for your build has become an issue, an experienced contract manufacturing partner like PEKO can help you manage your supply chain to get you the best possible outcome without the time and hassle.
4. Critical Parameters
Every machine has a purpose in life, and designing and manufacturing machinery requires the most technical considerations. Fundamentally, there are inputs, processing, and outputs associated with each piece of capital equipment. Defining the inputs seems easy, but there must be a well-thought-out process for this.
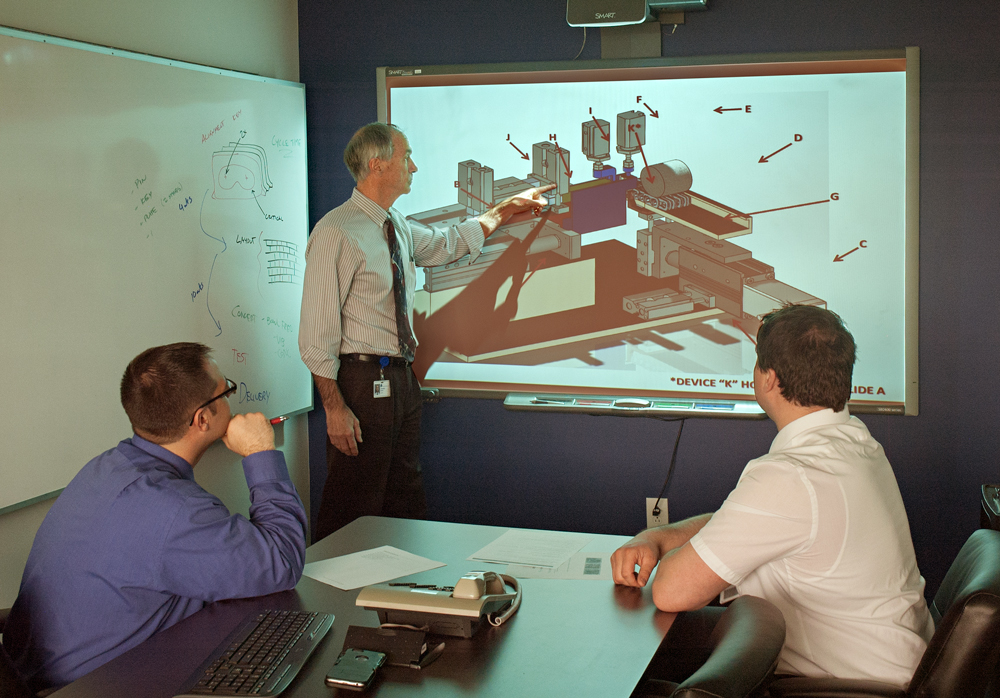
Inputs can be more than just materials and energy. There are human elements, environmental elements, and many more. Long before the manufacturing of your machinery begins, the designers must be thinking about the machine’s inputs. But of course, outputs are the end game. The machine has a final function that must be standardized, and the outputs must be defined with full clarity. When defining outputs, many questions may arise, such as:
- What are the outputs we are seeking to achieve?
- How are they measured?
- What is the rate of output?
- What are the violations of the outputs?
- What are some gray areas and how do we disposition them?
Overarching the inputs and outputs are noises and constraints. In any machine, you’ll find inevitable issues. One huge issue is not to violate physics. These days, many new technologies built into equipment are so cutting edge that through mechanics, software, or chemistry, they are pushing the bounds of what is physically achievable. Properly vetting these and synchronizing the theoretical and the realistic is critical at the time of design to ensure successful manufacturing that meets expectations.
5. Acceptance Testing
Finally, we arrive at the literal last step of the machinery manufacturing process: Factory Acceptance Testing (FAT). A well-defined factory acceptance test has to exist so all parties can agree on what is “good”.
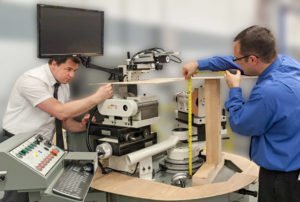
Factory acceptance tests usually involve powering up the machine and performing pre-defined steps to ensure it meets specifications. This might involve running a specified number of cycles and measuring the output against some range of expectations, measuring features, and checking electrical connections, buttons, and sensors. Because they are usually off-site from the customer, machinery contract manufacturers must maintain proper procedures and documentation so that the testing can take place exactly how the customer expects.
Whether you’re an OEM outsourcing your machinery builds to an equipment contract manufacturer or an OEM with a team of engineers and manufacturing folks, these pillars are universal. BOMs, CAD models, detailed prints, sourcing, critical parameters, and factory acceptance testing are at the heart of every build. In the future, we’ll be talking about how quality systems, regulatory compliance, and prototype manufacturing are all threaded into the process.
Download our self-assessment guide on outsourcing machinery manufacturing for a full look at how and why to use a contract manufacturer to build your next fleet of machinery, equipment, and hardware.